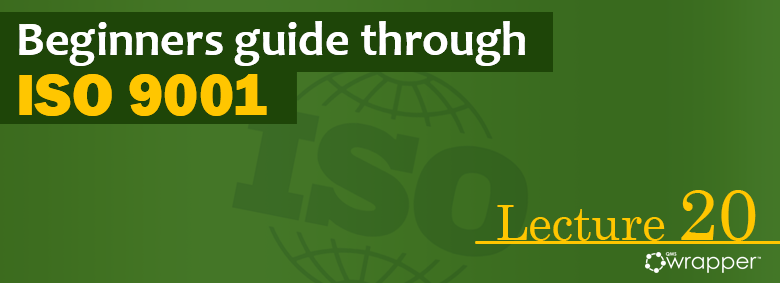
Control of Nonconforming Outputs – Lecture 20
Lecture summary:
- You must control nonconforming outputs in its processes, its products, or services.
- You should take appropriate action based on the nature of nonconformity and its impact on the conformity of products and services.
- You should also meet the reporting requirements of regulatory authorities for nonconforming outputs.
Treating and managing nonconformities is one of the basic objectives of the ISO 9001 Standard. Nonconforming outputs are the outputs of processes that don't meet a needed requirement or an expectation of one of the interested parties of the organization that are specified, implied, or obligated.
Controlling the nonconforming outputs is about planning activities for detecting nonconforming outputs and deciding what is to be done with them.
When you detect the nonconformance you have to document it. The document has to contain its description of the nonconforming output, what action is taken to manage it, etc.
Detecting the Nonconforming Outputs
Controlling the nonconforming outputs will allow you to minimize their effect. Be aware that they can appear in various places such as raw materials, components, goods that are in process or finished goods, or service operations. To effectively identify nonconforming outputs, you have to figure out which quality tools will show a process output nonconforming.
The ISO 9001 Standard requires quite a few controls as activities that may be of use:
- Verification activities
- Monitoring, measurement, analysis, and evaluation activities
- Control of external providers
- Release activities
- Audits and process audits
- Risk-based thinking
- Customer feedback
Reaction to nonconformity
As soon as nonconforming outputs are detected, you must react to them. The ISO 9001 Standard expects several basic actions for managing nonconformity. There are a few ways, and all of those can be implemented in QMS:
- Identification
- Segregation
- Correction
- Containment
- Informing the customer
- Suspension of the provision of products and services
Documenting a nonconformance
Documenting a description of the nonconforming outputs is required by the ISO 9001 Standard as documented information. We see this documented information as critical because it includes the primary information gathered about the nonconforming output and any information that would help you to investigate the nonconformity later on.
The information aims to assist you in mapping the problem and tracking down the root cause. Bear in mind that this documentation is the first step in a process that will later lead to corrective action.
PREVIOUS LESSON NEXT LESSON ALL LESSONS
ISO 9001 implementation: Mandatory documents and records
Continual Improvement and Nonconformity and corrective action – Lecture 24
Management review – Lecture 23