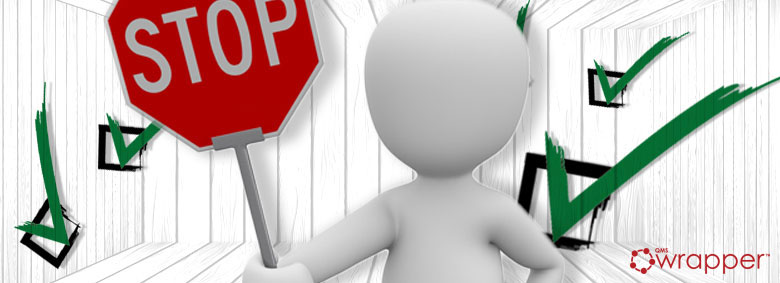
CAPA Checklist - Step by Step Guide
CAPA – Corrective action Preventive action
The purpose of corrective and preventive action is to collect and inspect information, identify and examine the product or potential quality problems, then take suitable and effective corrective/preventive action.
It’s a process of improvement taken to eliminate causes of possible malfunction, problems, or other unwanted situations. It’s also a process that auditor expects companies to follow.
It applies to manufacturers of medical devices and obligates them to include CAPA in their Quality Management Systems (QMS).
Besides its compulsory requirement, CAPA helps companies to enhance their quality system to reduce risks and avoid potential problems in the future.
There are 5 steps that are practical guidance for successful follow-up:
-
IDENTIFICATION - defining the possible or real problem, nonconformity, or incident, and describing the situation as it currently exists.
There are a few key questions to start with while deciding what problems need to be resolved.
- What is affected? (process, product or device)
- How often the problem might take place?
- What is its importance?
- What are the possibilities for it to happen again?
- Was it monitored and/or evaluated from different angles?
-
INVESTIGATION - determining the root cause of the problem, nonconformity or incident which involves collecting relevant data, investigating all possible causes and using the information available to determine the cause of the problem.
There is a good system of 5 Why’s (sample: package of a product)
- Why? – it takes a lot of unnecessary space
- Why? – because it’s irregular
- Why? – because the designer of a package made like that
- Why? – because he/she got wrong instructions
- Why? – lack of communication in the team
-
CORRECTIVE ACTION - actions taken to correct the problem.
This part of CAPA includes several points
- description of the desired outcome or how the problem can be fixed
- individuals responsible for carrying out corrective actions
- creating measurable and achievable solutions
- implementing actions and managing them to the solution
-
PREVENTIVE ACTION - actions taken to guarantee the problem will not repeat
- Reviewing the history of the problem
- Analyzing the problem that occurred and escaped
- Identifying and choosing how appropriate preventive actions
- Verifying preventive action and its effectiveness
- Implementation
-
VERIFICATION - verifying the implementation and completion of all changes, controls, and training.
Verifying the CAPA finishes the circle of identifying a problem and completing the actions to solve it. At this point, it’s important to make sure that the actions taken were effective.
- Audit method – applies when correction involved changes to a system
- Spot check – applies for random observations of performance or product
- Monitoring – used for real-time observation over the defined period
- Trend analysis - a retrospective review of data to verify that expected results were achieved
Replacing a paper-based CAPA process with an electronic system and connecting it with change control, training and other quality systems can help assure the problem can never be experienced again.
Zeba Franklin
|
Tracy Z.
|