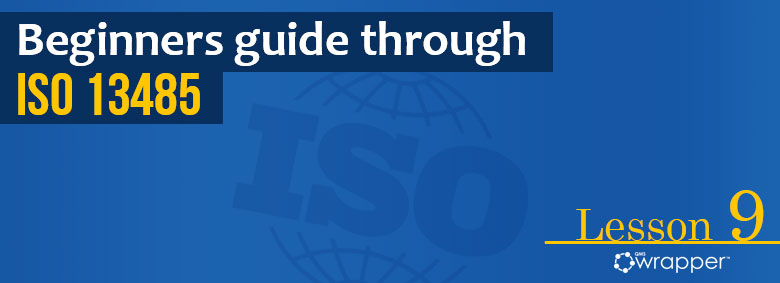
Work environment and contamination control according to ISO 13485 – Lesson 9
Work environment and contamination control are important and critical for effective and compliant medical device business run.
Definition of the Working Environment
Work conditions and environments must be under effective control. And by the ISO 13485 standard, it undoubtedly means, it must be documented as well.
It’s expected that the working environment will be in the proper conditions and realization processes that have a direct influence on the successful production of the medical devices. But the work environment is not just buildings, but equipment and materials used during production. It’s important to monitor working conditions in case you want to keep it on a certain level.
In most cases, the work environment consists of:
• Elements that may influence the processes and activities
• Physical elements of workspaces
• Resources invested in the processes or operate the activities in the workspaces
It’s critical to thoroughly understand the relationship between the product, employees, and facilities. By properly understanding these connections, it's going to be easier to properly identify the work environment. The following step is to review it. It means questioning and observations of employee’s activities, the analysis of their tasks, performance, efforts.
Clean environment - in this part ISO 13485 explains that is required to maintain documents for cleanliness or contamination control requirements for devices that are cleaned. The controls of the workplace and human resources have to be planned to correlate with these requirements. It has to support cleanliness goals.
Determination of the Contamination Control
In the medical device, the industry is expected that sterile medical products will come out from the manufacturer. If that wouldn’t be the case, the patient’s health could be endangered. Even potential contamination could cause serious harm to product performance, quality, and safety. That’s why the ISO 13485 standard emphasizes the importance of establishing, documenting, and maintaining contamination control.
There should be a specific procedure for all returned devices to avoid cross-contamination. Plus, they should be revalidated that they are in the identical condition as a new product, before being submitted to the work environment – intact and unharmed, and a package sealed and complete. The purpose is to ensure the status of these products is acceptable and that there is no risk of contaminating other products, work environments, or employees.
Contamination control must be planned, defined, and maintained using documented measures. Contamination control is usually managed by proper ventilation systems, dust collectors, and monitored through air quality tests.
PREVIOUS LESSON NEXT LESSON ALL LESSONS
Rajesh
|