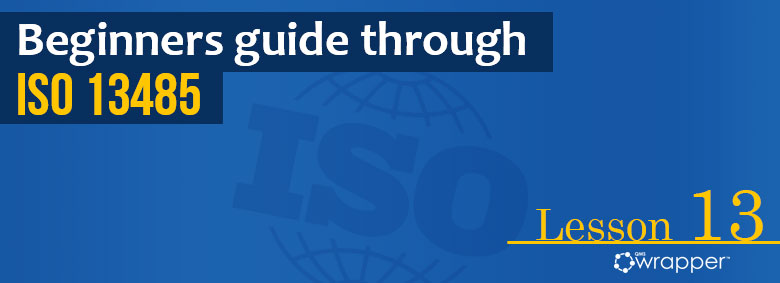
What is Purchasing process in design and development in ISO 13485 – Lesson 13
In the medical device industry, it’s not just purchasing. ISO 13485 standard has some strict rules when it comes down to purchase from suppliers. The main factors that influence this process should be addressed, and the main suppliers.
ISO 13485 requires you to document your purchasing procedure to ensure purchased products adheres to stated purchasing information. What does that mean? So, you are expected to create criteria for the evaluation and selection of suppliers.
The main point is that the medical device company describe how it will ensure the products will:
- Meeting predefined requirements and specifications
- Determining the appropriate controls over the suppliers
- Ensure the manufactured medical device is safe and effective as the standard requires
When it comes to the supplier evaluation, you need to establish a set of criteria for the selection and evaluation of new or existing suppliers, and also to evaluate the supplier’s ability to solve the non-fulfillment of an agreed purchase order.
The objective is to establish an ongoing control process over the supplier to foresee events that might become nonconformities or quality problems.
After you have evaluated the supplier, and have provided them with your feedback, you should, after a defined period, reevaluate whether or not they have improved their performance.
Purchasing information
The ability to transfer clear specifications regarding the product requirements to the supplier is essential. So, it should be ensured the information will contain the required details before delivery to the supplier.
The purchasing information must be reviewed and verified. It is necessary to determine a method for reviewing the purchasing information before submitting it to the supplier for execution. So, it should be ensured the information is clear, correct, and complete. The check should be carried out by an authorized person.
ISO 13485:2016 addresses the requirement to include written agreement notification by the supplier when it comes to the changes in the product that provides to the company. When your supplier needs to perform changes on the product, it must notify you in advance, and receive your approval. The issue should be discussed and agreed upon on an agreement or contract level.
Verification of purchased information
Consequently, you should verify the received product against what was agreed with the supplier. Your medical device company will define which product requirements will be controlled, specifications, characteristics, which areas, or issues on the purchased product are to be tested, controlled, evaluated, verified, etc.
The methods for conducting control activities can include testing, reviews, sampling, evaluation of services, etc. The point is that the selected method ensures the purchased product fulfill defined specifications and requirements, and that won’t be included in the realization process if it does not.
qmsWrapper provides a process for purchasing controls,
that make sure non-step will be missed when it comes
to this quality event. It will ensure the purchase order
contains all relevant data and it is approved,
the purchased product is verified against
defined criteria and ready to be released.
PREVIOUS LESSON NEXT LESSON ALL LESSONS
ISO 13485 implementation: Mandatory documents and records
Validation efforts
Gap analysis in QMS