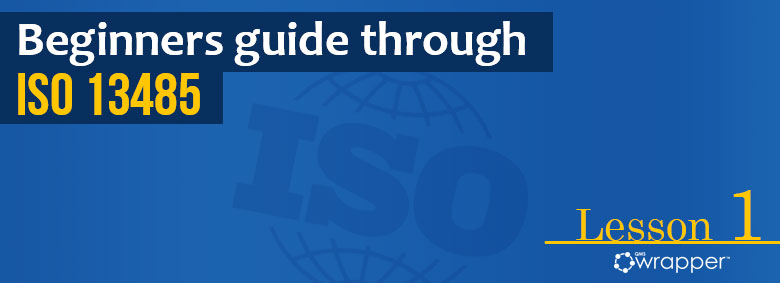
Understand ISO 13485 - Lesson 1
Let’s say you have an idea of placing an innovative medical device on the market. That’s great, but you already know that going from idea to actual realization is not the whole picture, just the tip of the iceberg. Yes, there is a much larger part below the surface to know about, and it has the name, it’s called ISO 13485.
“ISO 13485:2016 specifies requirements for a quality management system where an organization needs to demonstrate its ability to provide medical devices and related services that consistently meet customer and applicable regulatory requirements.” – as stated on its official website.
Or shortly: ISO 13485 2016 is a quality management standard for medical devices. It’s not a product standard, but a process standard. Therefore, it’s not enough to establish a QMS that complies with ISO 13485, you also need to comply with relevant product and service-oriented technical standards and regulations.
What this means and everything else in the standard, we will do our best to simplify it for you through this content step by step.
What are the QUALITY MANAGEMENT STANDARDS
The aim of these standards is to provide help to any organization that wants to meet product and customer requirements on a severer level. This way organization will be compliant with all regulatory and statutory requirements.
There are various definitions, but the essence is the same. You can look at it through many frames.
A quality management system (QMS) is a set of interconnected elements like:
- Using a process approach
- Handling the evidence to make decisions
- Managing your corporate relationships
- Encouraging improvement
- Engaging and involving staff
- Providing leadership in the organization
- Focusing on customers and involved parties
“qmsWrapper supports process and team-focused approach to QMS that ensures everyone works together towards desired quality outcomes.
The processes approach can reduce errors, forgotten paperwork, missed QMS reports. Your team is not guessing what to do next for compliance, it’s defined for them, monitored and managed by management automatically.
The continuous improvement, tracking and measuring of your operations inevitably lead to an increase in productivity and efficiency!”
Organizations can implement these to create quality policies and quality objectives. It can be used to establish the processes needed for ensuring policies are followed and these objectives are achieved.
It’s a system that supposed to if implemented right in the organization, improves your business processes, reduces your waste, lowers your costs, and much more. Simultaneously, it’s focused on customer satisfaction.
We can say it’s a set of interconnected activities that guide to the desired quality of products, customer and organization’s requirements.
ISO 13485:2016 – introduction
This is a standalone standard but it’s principally based on the structure of ISO 9001:2015. The ISO 13485:2016 additionally includes specific requirements like traceability, risk analysis and sterile manufacturing. Every organization involved in the MedDev industry must prove the ability to deliver medical devices and associated services that consistently meet customer and applicable regulatory requirements.
This Quality Management System compliant with ISO 13485 standard is mandatory for medical devices sold in the US, Europe, Canada, and other countries.
Purpose of the standard
The purpose of this quality management standard is to support medical device creators to need both: customer expectation and regulatory requirements.
Medical device organizations are using this standard to establish a quality management system for the design, development, production, and installation of medical devices and related services. The point is to prove their quality management processes and ensure the best practice in everything they do.
5 top benefits of implementing ISO 13485:2016
- INCREASING YOUR COMPANY’S CREDIBILITY AND BRAND IMAGE
It shows clients and customers that your company takes quality very seriously and that you have a system in place to ensure it.
- IMPROVING DECISION-MAKING
When you use facts and data to drive your decisions tend to be better aligned with the strategic goals of your company.
- INCREASING CUSTOMER SATISFACTION
Standard itself is a set of Quality management principles, one of which is ensuring customer satisfaction.
- BETTER EMPLOYEE ENGAGEMENT
The more your employees understand their roles in delivering quality products and services, the more engaged they are, which leads to increased efficiency and productivity.
- IMPROVING YOUR PROCESS
You’ll be able to identify and eliminate waste within and between processes, reduce errors, and avoid rework-facilitating greater efficiency and cost savings.
PREVIOUS LESSON NEXT LESSON ALL LESSONS
sugath
|
qmsWrapper
|
We're glad you're following our blog. Keep up with us.