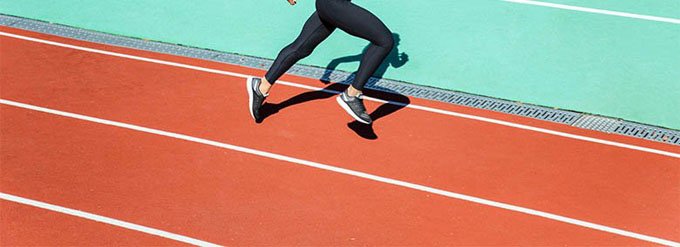
QMS for Beginners – A quick guide on where to Start ! …Part 2
The 13 items that will guide you through the implementation of QMS - continues...
4. Organizing the work
Next you will need to define the flow of how work gets done within your organization, i.e. the workflows. Why, because you need to understand where compliance issues will fit in. Workflows can show you the path tasks take through your organization… i.e. how things work, task by task.
A workflow process is a series of predefined tasks organized in steps, automatically initiated, and to be sequentially followed. Such workflows processes, help reduce work related errors and provide documented trails or records of what was done, by whom and when – ideal for compliance.
Most ISO’s are organized through workflow processes, and most Enterprise based QMS systems are workflow based systems.
What is important for you, is that Workflows and processes can include QMS rules and requirements defined as QMS events or issues or tasks.
In qmsWrapper, they are specifically called QMS Workflow-Processes and represent the easiest way of achieving Compliance.
In qmsWrapper, QMS Workflow Processes for ISO 13485 (2003), ISO 13485 (2016) and FDA QSR, are included.
Also, the Wrapper Workflow Process Editor allows you to create your own or edit/modify the existing ones to suit your particular needs.
This gives you the flexibility and power of an enterprise level system, ideally packaged for any small to medium sized company including Startups.
5. Software or paper based system
A recent survey in the USA determined that approximately 50% of the companies that had a QMS system, were still on a paper based system. The reasons were simple, they were initiated and installed at a time when paper was king and a change to an automated or computerized system would represent a major disruption – because change is hard. Still, the main reason for companies to migrate to a computerized system is usually related to either the increasing cost of personnel or lack of trained personnel.
"...the main reason for companies to migrate to a computerized system is usually related to either the increasing cost of personnel or lack of trained personnel."
The reality of today is that you should start with an appropriate QMS software, it’s easier than a paper-based system, and a system like qmsWrapper has all the rules and procedures for Compliance already built-in. Just add your own tasks.
That means you don’t have to be a highly qualified QMS expert with extensive QMS experience, you don’t need to know all the exact details of FDA QSR or ISO Standards for medical devices or ISO 9001 to stay compliant. An integrated QMS like qmsWrapper packages the expertise in its validated and verified for use QMS Workflow Processes. All you have to do is follow them.
Still, if your team consists of 2 person, paper forms and one file cabinet just might work.
Anything more, you’ll appreciate an integrated QMS system, like qmsWrapper.
6. Risk Management (RM) and Risk Analysis (RA)
Risk Management (RM) is the basis of FDA’s QSR and now of ISO 13485 (2016).
Both specifically refer to ISO 14971 for how to determine what is RM and how to do it.
So there is no ignoring RM! Whatever you select has to include RM as part of the solution. A Stand-Alone system can work as it helps you address the problems. But when RM is integrated into the Project Management, then it can create a history of RM issue for a project or sub-project that is Traceable and Trackable.
You seriously need to factor that into the plans.
7. Document Management & Control (DMC)
Many companies initially make the mistake of thinking a Document Management system is all they need to start with. After all, the proof of Compliance is a signed document! Right? Sounds logical and certainly it helps. But don’t kid yourself, it’s far from complete and far from easy. There is more to Compliance than a signed document and version control.
DMC is necessary but it is not enough for achieving compliance:
1. Many enterprise QMS system vendors, such as MasterControl, want you to believe that DMC is all a small company needs. They are trying to protect their high end and high priced systems. Document Management only systems are just that - Document management, they are not QMS. The simple DMC does not support the workflows. They do store documents well however.
2. The second problem for DM only solutions is knowledge. As a startup, you don’t know all the details required for Compliance. Sure, you read the ISO Standard, 100 times, but really, did you figure it all out? I’m going to take a wild guess here and say, not really! Your priority after all is the product and sales.
Face it, this is not just details we’re talking about, its red tape. You need help not just with DM but also with all the other details that lead to Compliance, including the How-To’s. A system that can guide you through this process, is worth its weight in developer hours… a.k.a. company cash.
3. Another example of a Forms based system is the PDF based systems. These types of Compliance systems initiate a “basic workflow” where a PDF form is circulated, usually by email, to designated assignee’s. These Assignee Users have to know what to do with it and, here’s the hard part, know exactly when to initiate it. Really, asking users to do an admin tasks – willingly! Good Luck with that!
Not being integrated into the real workflows, but bolted on, these types of add on systems depend heavily on outside triggers and user knowledge. Although they do handle documents well, initiating and getting the work and tasks that lead to the completed forms is lacking – let the paper chase begin.
There are many examples where the FDA looked past the “completed” form to the “work” that should have lead to that perfectly executed PDF Form. The problem is that when only the perfectly signed and completed form is found, and there is no supporting proof of the work, tasks, leading to that document. This is the point when the perfectly signed form usually gets shredded (i.e. you get an FDA deficiency letter).
Usually, it is only later that companies realize that besides a DMC, a project management software would be of great help as well.
And rarely are these separate solutions ever compatible with each other, being very vendor-specific, and usually very pricy when purchased separately. Now you’re stuck with two systems at twice the price and twice the fun!
To be continued ...
QMS for Beginners – A quick guide on where to Start ! …Part 1
QMS for Beginners – A quick guide on where to Start ! …Part 3
QMS for Beginners – A quick guide on where to Start ! …Part 4
A New Vision for Risk-Driven QMS with qmsWrapper
qmsWrapper Recognized as a Rising Star in the Spring 2025 Quality Management Software Customer Success Report
Enhancing Visibility and Accountability in QMS with qmsWrapper’s New Log Functionality