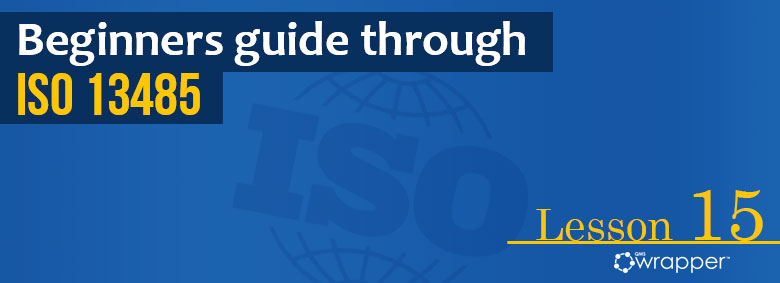
Control of monitoring and measuring equipment in the medical device industry – Lesson 15
The ISO 13485 standard treats monitoring and measuring devices very seriously. Every medical device company must have had plenty of various equipment for measuring and monitoring. According to the ISO 13485 Standard, they are considered as an important element of the realization process. Therefore, the requirements are quite specific and logical.
If you want your data or results to be valid, measuring equipment must contain the following elements:
- Has to be calibrated or verified before their use
- Has to be adjusted or readjusted, as necessary
- Has to be identified to determine its calibration status
- Has to be safeguarded from any potential risk or damage that might cause invalidation of the measuring result
Every medical device company has to have a documented procedure for equipment calibration or verification. Those have to be maintained regularly.
The Standard that covers this part is ISO 10012:2003 - Measurement management systems — Requirements for measurement processes and measuring equipment
Advice:
Record the equipment ID in every test related to incoming, in-process, and final inspections. Add guidelines in your SOP for equipment calibration and verification. Having the set procedure for this clause will make your life much easier. Define how measurement activities will be determined. Refer to issues like instructions, frequencies, areas, measured material, products, and processes. The procedure will define how the manufacturer sets the criteria for measurement results; for example, tolerances, limits, expected test results, customer requirements, regulatory requirements.
The issue of monitoring and measuring processes and products is one of the tools for the implementation of controls of risks and the measurement of their effectiveness.
Every so often you will have to trace back and recall products for remeasurement where the issue was critical.
The ISO 13485 takes the issue one step further and expects there to be guiding principles regarding the implementation and control of measurement and monitoring devices.
Monitoring and measuring equipment is a key role in their approval. According to the measurement result, it is decided whether the product met its requirements or not. However, you better prepare yourself for the possibility that monitoring and measuring devices will be found to be defective, inaccurate, with a malfunction, or not calibrated. This means there is a possibility that products that were released, based on measurements made with the defective devices, do not meet their requirements and specifications. When such a situation occurs, the manufacturer must evaluate the effect of the inaccurate measurement on the quality of the product.
Using qmsWrapper’s Custom form feature it is easy to build the template for recording the calibration activities.
It will be obvious that who and when performed it, therefore it's easier to follow up when the next interval of calibration shall be done.
PREVIOUS LESSON NEXT LESSON ALL LESSONS
ISO 13485 implementation: Mandatory documents and records
Validation efforts
Gap analysis in QMS